GoRound registreert kritische controlepunten bij brouwerij Lindemans
At the Lindemans Brewery, seven operators in two shifts use the GoRound app on their smartphone to register the results of the critical control point (CCP) inspections of the bottling line. This saves fifteen minutes per batch, says product manager Dimitri Pé.
This article is based on the article by Yves De Groote on the VMT food website
“Within the brewery we are highly automated, but until recently we were not familiar with digitalisation in the production environment,” says production manager Dimitri Pé at the Lindemans Brewery. The family brewery, founded in 1822, specialises in lambic and gueuze beer and is FSSC 22000 certified. “Ten years ago we implemented an ERP system for the logistics processes and then a SCADA system for control of production.”
Despite the extensive automation, checks by operators remain essential for product quality assurance, according to Pé. Examples are the pasteurisation effectiveness, the control of proper cleaning and the sorting out of unusable bottles, the proper sealing of the cap and the correct labelling. “In total, in the brewery for the filling of our beers, there are 6 critical control points (CCPs) that must be inspected by the operators. The total number of CCPs per bottling line is 4.”
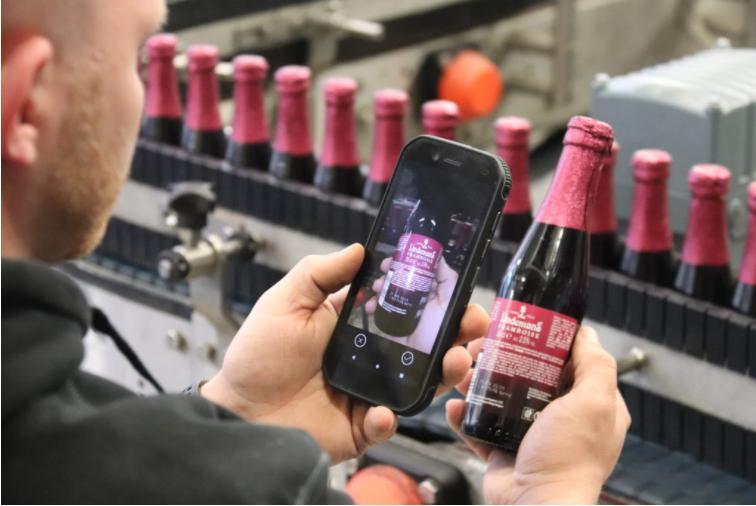
Pé: “In the meantime, we have been able to add numerous other quality checks that are constantly confirmed with a photo. This makes it easy to check later on how the coding was applied, what labels were used and what the quality of the box printing was.”
Until now, the operators note down the results of the inspections on various paper documents. After production, these are collected in order to release a batch after assessment. The employees on the line had no insight into the records at other locations on the line. With the GoRound app, operators and production managers can now see all the records made for the batch in real time on their smartphone.
With just the push of the button
“With the GoRound app from Gemsotec, we now generate clear daily reports of the quality checks of the average 21 batches per day by pushing a button. Per batch, this saves 15 minutes compared to before,” says the production manager. Besides the time savings, an important advantage of using the app is that documents and thus information are not lost. Finding all the information again is also very efficient.
"Per batch, this saves 15 minutes compared to before."
Dimitri Pé (production manager Lindemans)
The app also ensures that all inspections are done by operators. “If an operator does not record a test, a subsequent test by another operator cannot be entered,” Pé explains. “A batch can then also not be released. Team leaders keep an eye on this and employees also hold each other accountable in order to improve cooperation.”
Experience with smartphones
According to the production manager, the operators’ experiences are positive. “A few had less experience with digitalisation and were reluctant, but were triggered by their experiences with their smartphones.” Stefan Ruyters, co-founder of Gemsotec and responsible for innovation and technology, adds that working in a modern environment appeals to employees. “Especially with bottleneck profiles like STEM, it is important to stand out as a company.”
Production chain
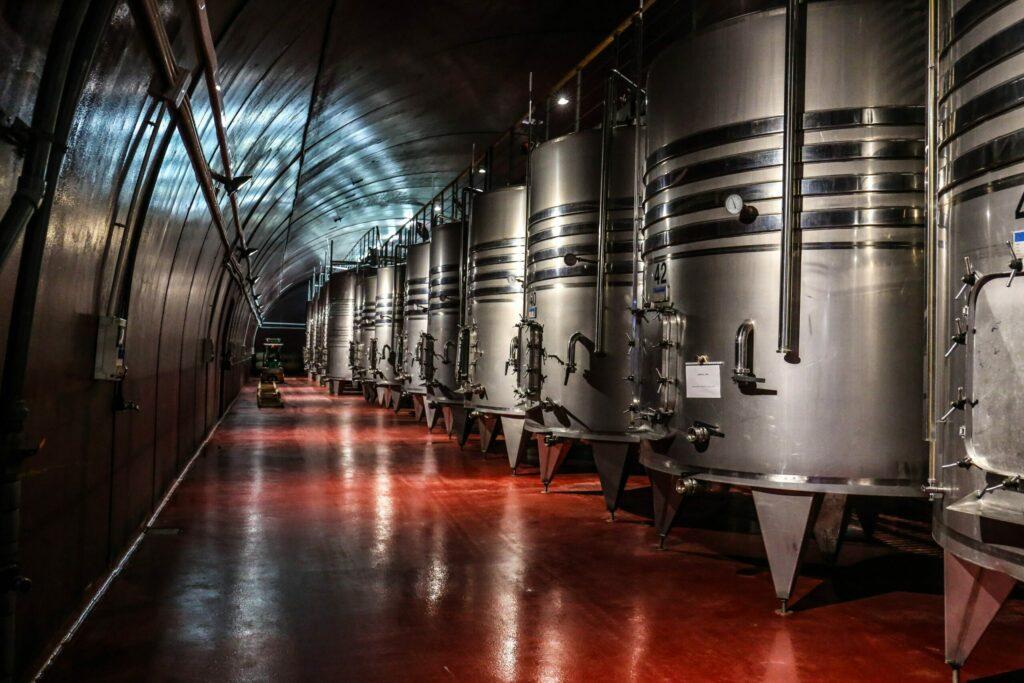
The production manager says that in the future, the app may be used for the entire production chain, so that all data will be traceable. It is certain that the app will be expanded with a maintenance and cleaning module to streamline these activities within the brewery. Naturally, a test phase will be planned beforehand, as is also the case for quality control.
“GoRound is a SaaS (Software as a Service) cloud solution completely tailored to the user,” explains Ruyters. “The existing paper registration forms can easily be put together by the customer using the flexible configurator and the range within which a value must be registered can be filled in. Gemsotec helps the customer with this, especially with a view to future KPI dashboarding and analysis. After all, it’s important that the right parameters are configured in the right way in GoRound, so that later a dashboard can easily be created with ‘actionable’ insights”.
The GoRound app also works offline. Extra attention was paid to this when setting up the GoRound infrastructure in the cloud, Ruyters explains. “If the wifi network fails and a 4G or 5G connection is not available, operators can continue to use the app offline, Ruyters reassures. “Once the internet or 4G connection is possible, the data will automatically be synchronised, without any action required from the user. That is exactly what a SaaS application should do, completely unburdening the customer in terms of ICT.
Communication
The app and the structured, multi-channel Microsoft Teams app work particularly well together for online communication within the company. From the GoRound app, a reported issue, e.g. an oil leak on a machine, can easily be shared with colleagues. In this way, the observation and photos taken can be posted and someone can quickly be asked to carry out a repair. Thanks to the photo, a good view of the situation can immediately be formed and the right material for the repair can immediately be brought, Pé explains.
“Previously, operators used different Whatsapp groups for mutual contact on their own initiative without consulting their managers, but as a company you don’t want that, because you have no control and insight into it here.” Thanks to integration with the GoRound app, users are encouraged to use Teams.
QR-codes on machines
A total of one hundred QR codes have been applied to the machines in the brewery, including the bottling line. Each machine at Lindemans has its own specific maintenance and cleaning procedure. This results in over 150 checklists in GoRound. To quickly find the right checklist, the user scans the QR code with the GoRound app.
"This automatically starts the right checklist, which is a huge simplification for operators and technicians."
Dimitri Pé (production manager Lindemans)
Thus, the correct checklist is started automatically, which is a huge simplification for the operators and technicians compared to the current Excel list. Also, operators are sure to have the latest version of the checklist, whereas previously old versions of paperwork were lying around in production. In addition, manuals, spec sheets and other documents concerning the machines are also available at the GoRound app.
This project received a subsidy from S3food (s3food.eu), a European Horizon2020 project that supports SMEs with their digitalisation plans. This project was selected for an ‘exploration voucher’ out of more than 120 proposals.